Filtrer par genre
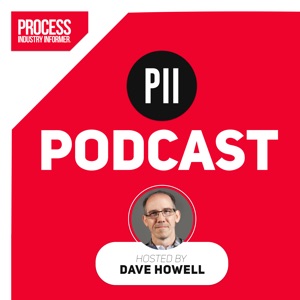
- 32 - Pioneering the future of Process Analysis
"Sensors are great, but they have their limitations" - that’s where analysers come in!
In this episode, Paul Hamilton from Metrohm discusses simple and innovative ways for Process Engineers to perform complex chemical analysis. Metrohm is best known for producing analytical laboratory hardware and software, but Paul explains how the process analysis side of the business brings all of the typical laboratory analysis techniques and integrates them into the process plant, producing lab-quality data in the plant, fully automated.
Compared to some other countries, the UK is behind when it comes to the process industry, but there is a shift happening, and now is the time to innovate and automate. There are countless ways in which a process can be automated, and most people don’t even realise it! A lot of companies are reliant on intermittent data from a lab, and that creates a bottleneck. Whereas automating your process provides real-time detailed data, which allows you to be proactive and make fast and accurate decisions; this, in turn, eliminates downtime, reduces costs, and raises efficiency.
Paul discusses real-life examples of companies and industries that have embraced automating their process and the results they have seen... often automation is much simpler than people think! Paul talks about how you can retrofit an analyser into your process, and how surprisingly easy that can be.
Lastly, Paul talks over what’s next for the process industry... spectroscopy?...
Don’t miss this insightful and eye-opening episode!
Wed, 03 Apr 2024 - 29min - 31 - Radial Insert Ball Bearings technology
For machines in the food industry, you need special solutions. Extreme temperatures, high mechanical loads, short cycle times, round-the-clock operation, and regular cleaning cycles require very robust components. Strict food safety regulations pose as much of a challenge here as efficiency and sustainability. Whether it’s for process automation in food production, for beverage production or the packaging industry, in all cases you need food-compatible rolling bearings, plain bearings, and linear guidance systems as well as adapted lubrication and seal concepts. Even during the planning stage of your machines, it is already important to find the right rolling bearing solution for your application, for example with the aid of simulation tools. And with permanent condition monitoring, you create the best conditions for the reliable, hygienic, and economical operation of your equipment. Learn more about how you can successfully meet the challenges of the food, beverage, and packaging industry. In this podcast we are considering Radial Insert Ball Bearings technology and also Scheffler's condition monitoring technology, Optime. My guests today are Tom Richmond, Scheffler’s Food and Beverage Sales Engineer and Sally Sillis, Shefler Technical Manager.
Topics include:
What makes Radial Insert Ball Bearings technology particularly applicable to the Food & Beverage industry. Overview of Scheffler's condition monitoring technology, Optime and its core principles. How Schaeffler’s Condition Monitoring services and technologies support customers. How important is FDA certification. How Schaeffler is involved with the design stage of a new process, or helping customers to evolve existing systems and processes. An outline the sustainability credentials of Optime and Radial Insert Ball Bearings technologies.
Why contact bearings or combined radial and axial loads are particularly applicable to the food and beverage industry. How Optime can be integrated into existing machinery and control systems.
Thu, 28 Mar 2024 - 26min - 30 - How interface measurement could transform your business
In this episode of the PII Podcast, we delve into the world of interface level measurement, concentrating on those difficult multiphase applications with dynamic emulsion layers. The key to optimising performance in these situations is solving the emulsion factor – a hurdle that has long stood in the way of accurate and economical level detection. Traditionally, no single technology has been able to economically measure the total hydrocarbon level, the top of the emulsion (where water mixes into oil), and the bottom of the emulsion layer, (where oil mixes into water). This multiphase scenario has challenged many traditional technologies, each of which faces its own limitations. Despite the considerable efforts from instrumentation manufacturers, a truly cost-effective solution has been elusive... Until now. Today we are exploring TDR-based technology and how this is changing the game. Learn the science behind it, and what it means for the future of industries reliant on precise level measurement. To unpack all of that and give us his expert insights,we are joined by Bob Botwinski - a Senior Global Product Manager for AMETEK LMS.
Tue, 19 Mar 2024 - 33min - 29 - 3D level measuring technologyThu, 11 Jan 2024 - 28min
- 28 - Cote-Shield Technology
AMETEK Drexelbrook's "Cote-Shield" technology revolutionises point level detection in tanks and vessels by effectively ignoring conductive coatings on the sensing element, ensuring a reliable, repeatable measurement and maintenance-free operation. This technology overcomes the common issue of false alarms caused by process coating buildup that can cause false alarms potentially interrupting the critical process and costing loss in profits. Cote-Shield addresses this issue by introducing a three-terminal style probe design that incorporates a Cote-Shield element, that ignores process coating buildup and prevents false alarms. This innovation enables Drexelbrook's level devices to function reliably, even under the most challenging process conditions. Preventing these types of failures can help save on preventative maintenance, automate your process, and save money. Renowned for their reliability, Drexelbrook's level devices equipped with Cote-Shield technology have been deployed in more than 100,000 systems around the world. They are known for delivering consistent results even in harsh conditions and are relied upon by industry leading companies across the globe.
Tue, 28 Nov 2023 - 28min - 27 - The importance of having an accurate and reliable calibration solution
In this podcast from Beamex, we talk about the importance of providing accurate measurements, reliable data and traceability when performing instrument calibrations. We’ll explore how the digitalisation of data helps to improve operational efficiency for optimal asset performance, with examples of industries where calibration occurs, particularly looking at how National Grid has been able to reduce costs and improve efficiency of their calibration processes.
Mon, 24 Jul 2023 - 38min - 26 - Improving bulk material management through cloud inventory and continuous level sensors
In this podcast, BinMaster’s Regional Vice President of Sales Mike Mossage shares how processing industries can benefit from cloud inventory, the use of continuous level sensors, and the application of Industry 4.0 in making bulk material management more efficient. For more than a decade, Mike has helped industrial manufacturers across diverse industries solve their most complex bulk inventory issues and make peoples’ jobs easier.
Thu, 05 Jan 2023 - 30min - 25 - The manufacturing industry's status and growth
The importance of robust, integrated, and secure CQV services in all industries, emphasizing pharmaceuticals. In the past three years, the global manufacturing process scale-up to support the COVID-19 vaccine development led to a complete transformation of best manufacturing practices across all industries. In this podcast, CAI's Director of UK Operations Zagros Barazenda shares the best practices in operational readiness from his experience consulting in cGMP Biomedical, laboratory, and Biotechnological environments. Most recently, he facilitated the relationship between a global-leading COVID-19 vaccine developer and a brand manufacturing facility site to complete a typically 3-5 year project in one year. Shifting from a chronological to an integrated approach – where quality assurance, automation, and engineering professionals are present in every phase – can help your production facility improve efficiency and ensure a seamless path to market. Topics include:
How a risk-based approach in the discovery phase can reduce deviations throughout the project's lifecycle How COVID-19 is changing manufacturing processes and operations – through the evolving workplace, adopting automation and AI, and new compliance standards How big players in the pharmaceutical industry are now outsourcing to CMOs The tell-signs a facility is not meeting government audit regulatory and compliance standardsTue, 29 Nov 2022 - 36min - 24 - Celebrating 20 years of great partnerships that deliver for ABB customers
In this latest podcast Dave speaks with Scott Kirk, Industrial Sales Manager for ABB Measurement & Analytics UK & IE. Here Dave discusses with Scott the value of building strong relationships with channel partners and distributors and all of the benefits that partnership delivers for customers of ABB products up and down the country.
Topics include:
- How ABB approaches partnerships to ensure goals are achieved - How the ABB Value Provider works and what advantages it delivers - What is the core value of becoming an ABB Value Partner - Examples of clients using the ABB Value Provider service - How ABB helps its partners stay current with changing trends in measurement and analytics - Transformative changes in the way businesses use instrumentation - Predictions for future measurement and analytics - How will the ABB Value Provider program evolve into the future
Wed, 16 Nov 2022 - 27min - 23 - Smart recipe handling to transform manufacturing capabilities
Recipe control is a very specialist field that applies to a wide range of industry sectors. The data collected by a well designed recipe handling process control system can give deep insights into all aspects of production.
Recipe control can also function as a quality control method or more accurately risk control when the product being made has to meet defined standards and need to be as reliable as possible for incorporation in to end user's finished products.
In this podcast Charles Williams discusses recipe control from his experience in multiple industries. Charles is second generation in Promtek Ltd, a family owned business in the heart of Stoke on Trent.
Trusting the data in your recipe control system is one of the most important steps you can take to unlock the potential to improve efficiency, sustainability and quality control for your production facilities.
Tue, 19 Jul 2022 - 39min - 22 - Seeing the future health of industrial manufacturing production assets
Unplanned downtime in industrial manufacturing causes productivity loss, timeline delays and lost revenue – estimated at around $50 billion each year. To address this tremendous market problem, PARC, a Xerox Company, recently launched Novity, a new venture to commercialise predictive maintenance technology. The technology solution uses equipment sensors and proprietary algorithms to enable industrial manufacturers to see the future health of their production assets. The Novity TruPrognostics™ engine relies on a combination of machine learning and physics-based models of equipment, allowing it to predict failures with 90% or better accuracy and lead times of months, not weeks or days. In this episode, Dave speaks with Markus Larsson, General Manager and founder of Novity about the pioneering technology and what it means for the future of industrial manufacturing.
Wed, 04 May 2022 - 36min - 21 - The impact of chemical shortages on water treatment
In this episode Dave speak with Robert Stancombe, Business Development Manager of Veolia Mobile Water Services.
Power plant operators are increasingly looking at ways to optimise the use of water in steam and cooling cycles in thermal power plants. However, implementing new technologies can present challenges. Robert Stancombe of Mobile Water Services discusses how the use of mobile reverse osmosis assets can help streamline the implementation process and help operators who are increasingly exposed to high chemical costs and supply shortages.
Discover the many advantages of reverse osmosis upstream of a demineralisation plant for high-pressure and cooling water applications and the benefits of using a temporary system. A growing number of plant operators have already gone mobile with the implementation of a reverse osmosis pilot. Better system efficiency, cost savings and reduced environmental impact have even convinced some to extend the mobilisation of the reverse osmosis asset to last a number of years without the need for investment in fixed plants.
Wed, 27 Apr 2022 - 28min - 20 - How Digital Technology is Advancing Maintenance and Predictive Maintenance in the Process Industry
Finding new ways to solve customer problems has always been at the core of ABB Measurement & Analytics’ approach to product development. With the global focus on emissions and sustainability, industries are under even more pressure to increase the agility and reliability of emissions monitoring in real time. ABB’s Datalyzer is an application that has been developed to help customers respond to this challenge.
The solution offers enterprise grade, comprehensive, cloud-based analyser fleet monitoring, unlocking the value of asset data through actionable insights.
Join ABB Measurement and Analytics Digital Lead, David Lincoln, as he discusses how such tools remove complexity by transforming data into valuable business insights, not just for emissions monitoring but for all process industries looking to maximise uptime.
Tue, 26 Oct 2021 - 38min - 19 - Digital Transformation Strategy in BEUMER Group
BEUMER Group has declared digitisation a top priority to secure its own future viability. But how can this be achieved? How can a company that has been operating mechanical engineering as its core business for around 80 years push digitisation to its full extent? To get fit for the future, BEUMER Group is relying on two spin-offs which - with the support of start-ups - are to carry digital projects into the group company.
As a result of extensive research, two spin-off companies to complement the existing innovation department have been started; The BEAM GmbH was established in Berlin as an autonomous company builder and BG.evolution was established in Dortmund and aims to develop 'Minimum Viable Products', which are minimally equipped prototypes tested as possible solutions for a concrete customer problem.
In this fascination episode Dave speaks with Dr. Johannes Stemmer explains how BEUMER Group approached this transformation
Mon, 27 Sep 2021 - 40min - 18 - How breweries can become more digital
In our latest Podcast Dave speaks with GEA’s Hassan Yaszdi, Senior Product Manager Digital Service, and Dr. Mark Schneeberger, Head of Development of GEA’s Beer and Alcoholic Beverage Business and brewmaster, about how GEA is paving the way for breweries (and possibly other industries, too) to become more digital with their game-changing software
Over the next five to ten years, more and more new Industry 4.0 technologies will transform the production landscape of many industries - from connectivity to advanced analytics, robotics and automation. In the future, breweries will also be able to go paperless, monitor processes seamlessly, be notified of adjustments at any stage of the brewing process, and ultimately make changes with minimal human intervention. Such advanced monitoring software is now real - and more than that, it's on its way to becoming an auto-optimisation programme.
The ability to optimise a production unit in the future will depend on accurate, insightful and actionable data. However, many breweries lack the granular performance data necessary to take full advantage of digitisation and automation. This is where GEA's brewing and service experts come in, and they have now formulated an answer together with customers: GEA InsightPartner Brewery.
GEA InsightPartner Brewery is the first step, actually being in release phase 2 (for a whole brewhouse) at a customers site (Störtebeker Brewery in Germany). Future releases incorporating further process steps are in preparation. And best news: The GEA OptiPartner Brewery (which is the big brother of GEA InsightPartner) is no dream anymore, but already in the testing phase at a customer site.
As you will learn, whilst GEA InsightPartner gives brewers the knowledge to track and respond to their processes, GEA OptiPartner Brewery automatically handles end-to-end process optimisation for each brew, it really is a truly insightful listen….
Thu, 22 Jul 2021 - 38min - 17 - Remote access and management systems for the chemical industries
In this final episode of our 3-part series with Siemens, Dave speaks with Ian Poulett, Business Manager - Industrial Communication, RTLS & Identification, who discusses the types of systems used to manage networks and process systems.
Topics include:
- Management and control systems - How remote access and management can be achieved - How remote access, communications, management, and control can be applied to new digital systems - Digital transformation roadmaps - Security for remote access and control - How 5G will transform process management - Training and education of the digital transformation - What the future of remote access and management looks like
Tue, 20 Jul 2021 - 38min - 16 - What Industry 4.0 means to the chemical industry
In this second of our 3 part series with Siemens, Dave speaks with Dave Adams, Team Leader - Process Specialists.
Drawing on his 30+ years of experience working at Siemens, Dave provides an interesting insight into how the chemical industries are adopting industry 4.0 technologies.
Topics include:
Understanding and implementation Industry 4.0 in the Chemical Industries
Can fully automated or autonomous systems be used by plant managers across the chemical sector?
Does Industry 4.0 open the door to efficiency and cost savings
Analysing data for control and predictive analytics
How businesses can create a new digital ecosystem across their processes
First steps a chemical company should take to harness IIoT, edge computing and AI (machine learning)
Tue, 13 Jul 2021 - 36min - 15 - Air Gap Systems and Cyber Security for the Chemical Industries
In the first of a 3 part Podcast series with Siemens, Dave speaks with Paul Hingley the Product Solution & Security Officer GB&I at Siemens Digital Industries Software.
Cyber security is a major concern throughout industry and in this podcast Paul discusses concerns over air gapped systems in the chemical industry and alternative solutions.
Wed, 30 Jun 2021 - 38min - 14 - Monitoring and control systems for the water sector
In this episode, Dave speaks to data analytics software leaders from technology provider Ovarro, Alan Cunningham, subject matter expert, and Josh Britton, global product line manager.
As a major supplier of monitoring and control systems to the water sector, Ovarro is fully versed in the challenges faced by global utilities today.
Data and analytics, if applied correctly, can transform how water networks are managed, helping to ensure the environment is protected, regulatory targets are met and company performance is improved.
Alan and Josh discuss the current data landscape for water, and the innovation behind their software products such as AlarmVision, a cloud-based dashboard that enables control rooms to manage the stream of incoming alarms in real time.
Thu, 20 May 2021 - 37min - 13 - A true IIoT solution for automated valves
In our latest Podcast, Dave speaks with Remco Bakker, Business Development Manager of Imtex Controls, who discusses the introduction a new pioneering product; the Valvescan Diagnostic Monitoring System.
Remco explains how the VDMS provides a technological step-change in valve health monitoring for various process industries.
With the development of the Valvescan Diagnostic Monitoring System – an-end-to-end solution that captures data from every valve operation, analyses it and provides targeted alerts on the valve health without any requirement for involvement from plant personnel or any potential impact on the asset real time control integrity. It is a true IIoT solution for automated valves
Tue, 16 Feb 2021 - 30min - 12 - What is self-service advanced analytics?
You may read about digitalisation, Industry 4.0, Analytics, IIoT, Data driven decision making, and other related topics almost daily. The more you see these topics pass by, the more diffused it may have become.
In this podcast Dave and Thomas explore the basics about these topics and how operational experts can easily start with analytics without having to become data scientists.
Thu, 05 Nov 2020 - 28min - 11 - Think Sealless Pumps
Here Dave Howell speaks with David Clark, Senior Engineering Manager at HMD Kontro Sealless Pumps, who traces the evolution of magnetic drive sealless pumps, from their introduction 70 years ago to the very latest developments and materials that are driving the industry forward.
A step-change in design, driven by technology advances and innovative materials has seen the emergence of a new level of agility and flexibility while future-proofing products against ever-more stringent regulations.
Thu, 15 Oct 2020 - 35min - 10 - Single Pair Ethernet
Single Pair Ethernet is the technology that makes it possible to implement the Internet of Things consistently within industry, right through to field-based applications. Here, Dave speaks with Simon Seereiner, Head of Product Management for SAI and Industrial Ethernet at Weidmüller, who explains how Weidmüller are using this technology and the range of benefits it offers.
Mon, 07 Sep 2020 - 35min - 9 - Using Analytics to Accelerate the Digital Transformation of the Pharmaceuticals Industry
In this latest podcast, Lawrence Clark, VP Regional Sales, EMEA and Richard Porter, Senior Manager of Area Sales for EMEA, both of AspenTech, talk about how the company’s predictive analytics and asset performance management solutions can drive the digital transformation of the industry by optimising assets to run safer, greener, longer and faster. Lawrence and Richard discuss how these technologies can help pharmaceuticals manufacturers ensure security of supply, guaranteeing that customers have drugs available to them when they are needed, bringing tangible operational efficiencies and helping them avoid too much time spent on data science experiments that don’t bring a business benefit.
Mon, 17 Aug 2020 - 49min - 8 - Dave Howell talks with Alan Hunt, Electromagnetic Flow Product Manager at ABB
In this latest podcast Dave speaks with Alan Hunt, ABB Product Manager UK & IE – Electromagnetic Flow. Here Alan discusses issues around water use and water conservancy and his passion about what he calls the “Holy Trinity” of water sustainability.
Water companies themselves are saddled with the burden of matching supply with demand, but we as consumers both as process industry consumers and as individuals all must play our part in reducing consumption and ensuring the waste we discharge into water courses is meets or exceeds regulatory minimum quality standards.
The holy trinity covers;
Leakage – how to reduce the 3.1billion litres of water that are lost daily from the water network
Environment – how do we collectively ensure that water we discharge into water courses is not going to pollute it. What is the impact of MCERTS
Responsibility – it is up to us all to ensure we have enough water to sustain demand. The desire to be a good neighbour/good citizen now extends to company values
Thu, 06 Aug 2020 - 43min - 7 - Dave Howell talks with Patrick Deruytter Vice President Customer Care & Large PMO Emerson Automation Solutions
In this latest podcast, Patrick Deruytter, Vice President of Customer Care and Large Projects at Emerson, talks about the acceleration of digital engagement and how it is changing the way we work. Patrick discusses the new reality where work is done anywhere – and how extreme collaboration, speed of interaction and “anytime – everywhere” expectations are driving this shift.
Mon, 06 Jul 2020 - 32min - 6 - Dave Howell talks with Stephane Vanouche at EmersonFri, 22 May 2020 - 36min
- 5 - Dave Howell talks with Daryl Cowlan Sales Specialist at Weidmüller
In this latest podcast, Daryl Cowlan, Printing Systems and Tools Specialist at Weidmuller UK talks about how Weidmuller’s Workplace Solutions take customers through the phases of panel building, from planning to installation to operation, with optimally coordinated solutions for their workshops. He will explain how these solutions can vastly speed up work processes, and increase quality of work through the standardisation of workplaces, intelligently combined equipment, quick identification of tools along with integrated uses of configuration, marking software and the fast delivery service that can be used.
Fri, 15 May 2020 - 29min - 4 - Dave Howell talks with Glenn Schulz, FDT Group, Managing Director
Here, Glenn discusses the exciting latest developments about how the FDT Group have launched their latest digital transformation for the industrial automation sector with its’ new FDT 3.0 (FITS) standard. The new FDT IIoT ecosystem empowers scalable, skid-to-cloud solutions and innovative business models unlocking universal device integration with mobility and remote access for the new era of automation. Learn more about the enhanced offerings with FDT 3.0 by listening to this Podcast.
Tue, 26 May 2020 - 35min - 3 - How to become a truly data-driven plantThu, 23 Apr 2020 - 25min
- 2 - Dave Howell talks to Steve Leech at Siemens Digital Industries
Steve Leech, Business Manager for Process Control Systems at Siemens, talks about the acquisition of operational data from existing or new installations, and the application of it to optimise plant operation and maintenance. Steve talks about the vision, the practicalities, and the technical know-how to get the most out of smart instruments now, and how this lays the foundations for a digital plant.
Mon, 30 Mar 2020 - 28min - 1 - Dave Howell talks to Jamie Clayton at Freeman TechnologySat, 01 Feb 2020 - 25min
Podcasts similaires à PII Podcast
Global News Podcast BBC World Service
El Partidazo de COPE COPE
Herrera en COPE COPE
The Dan Bongino Show Cumulus Podcast Network | Dan Bongino
Es la Mañana de Federico esRadio
La Noche de Dieter esRadio
Hondelatte Raconte - Christophe Hondelatte Europe 1
Curiosidades de la Historia National Geographic National Geographic España
Dateline NBC NBC News
財經一路發 News98
La rosa de los vientos OndaCero
Más de uno OndaCero
La Zanzara Radio 24
L'Heure Du Crime RTL
El Larguero SER Podcast
Nadie Sabe Nada SER Podcast
SER Historia SER Podcast
Todo Concostrina SER Podcast
安住紳一郎の日曜天国 TBS RADIO
アンガールズのジャンピン[オールナイトニッポンPODCAST] ニッポン放送
辛坊治郎 ズーム そこまで言うか! ニッポン放送
飯田浩司のOK! Cozy up! Podcast ニッポン放送
吳淡如人生實用商學院 吳淡如
武田鉄矢・今朝の三枚おろし 文化放送PodcastQR